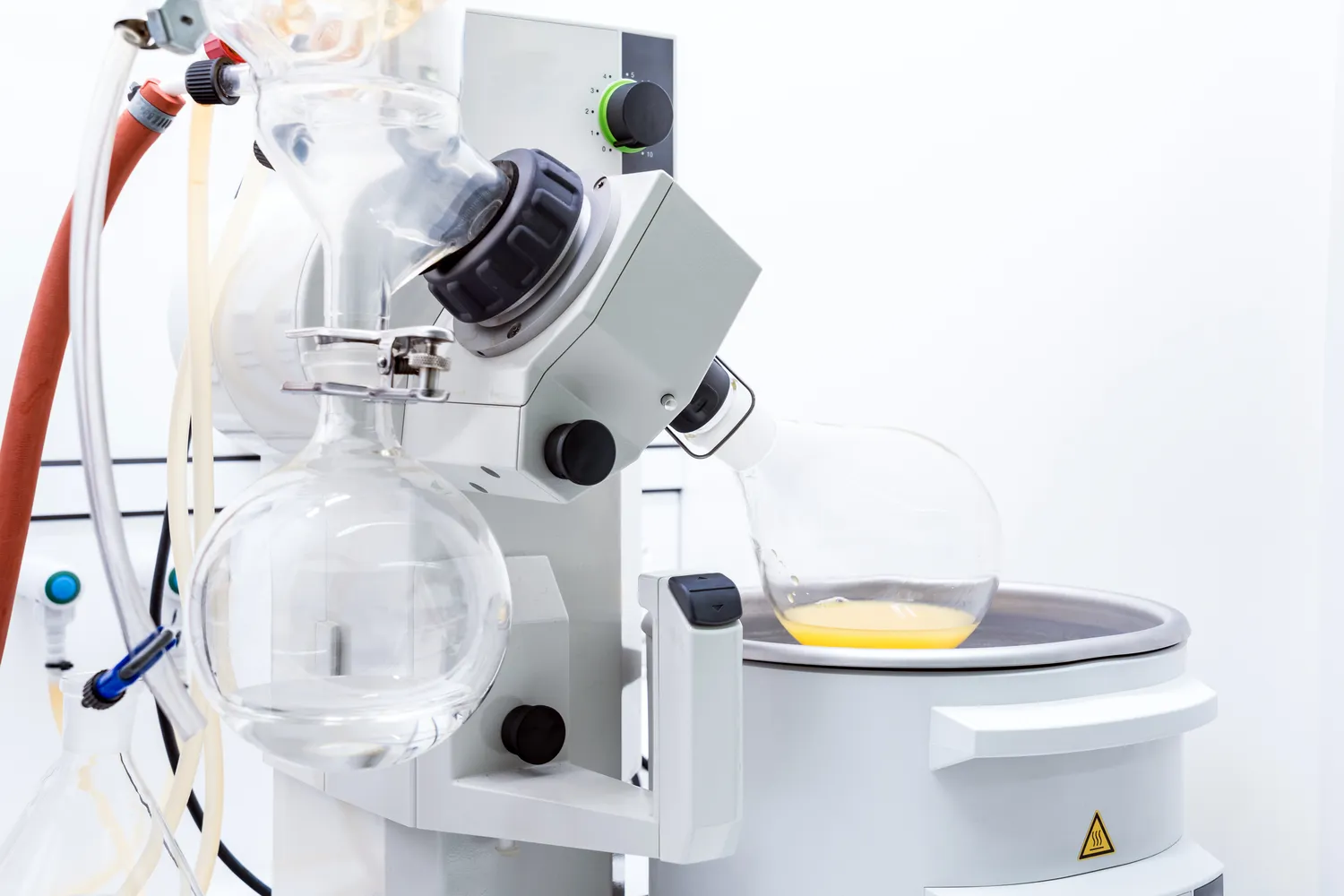
Destylator przemysłowy to urządzenie, które służy do separacji składników cieczy na podstawie różnicy w temperaturach wrzenia. Proces destylacji polega na podgrzewaniu cieczy, co powoduje jej parowanie, a następnie skraplaniu pary w celu uzyskania czystego produktu. W przemyśle destylacja jest kluczowym procesem wykorzystywanym w produkcji alkoholi, olejów eterycznych oraz różnych chemikaliów. W destylatorze przemysłowym można wyróżnić kilka podstawowych elementów, takich jak zbiornik do podgrzewania cieczy, kolumna destylacyjna oraz skraplacz. Zbiornik jest miejscem, gdzie następuje podgrzewanie cieczy, a kolumna destylacyjna umożliwia separację par w zależności od ich temperatury wrzenia. Skraplacz natomiast odpowiada za schładzanie pary i jej kondensację z powrotem w ciecz.
Jakie są rodzaje destylatorów przemysłowych i ich zastosowania
W przemyśle istnieje wiele rodzajów destylatorów, które różnią się konstrukcją oraz zastosowaniem. Najpopularniejsze z nich to destylatory prostokątne, kolumnowe oraz frakcyjne. Destylatory prostokątne są najczęściej wykorzystywane w małych zakładach produkcyjnych, gdzie nie ma potrzeby uzyskiwania dużych ilości produktu. Kolumnowe destylatory charakteryzują się bardziej skomplikowaną budową i są stosowane w dużych zakładach przemysłowych do produkcji alkoholi czy chemikaliów. Destylatory frakcyjne natomiast pozwalają na separację wielu składników jednocześnie, co czyni je idealnymi do procesów wymagających uzyskania różnych frakcji substancji. W zależności od branży, w której są wykorzystywane, destylatory mogą mieć różne parametry techniczne oraz rozmiary.
Jakie są zalety korzystania z destylatorów przemysłowych
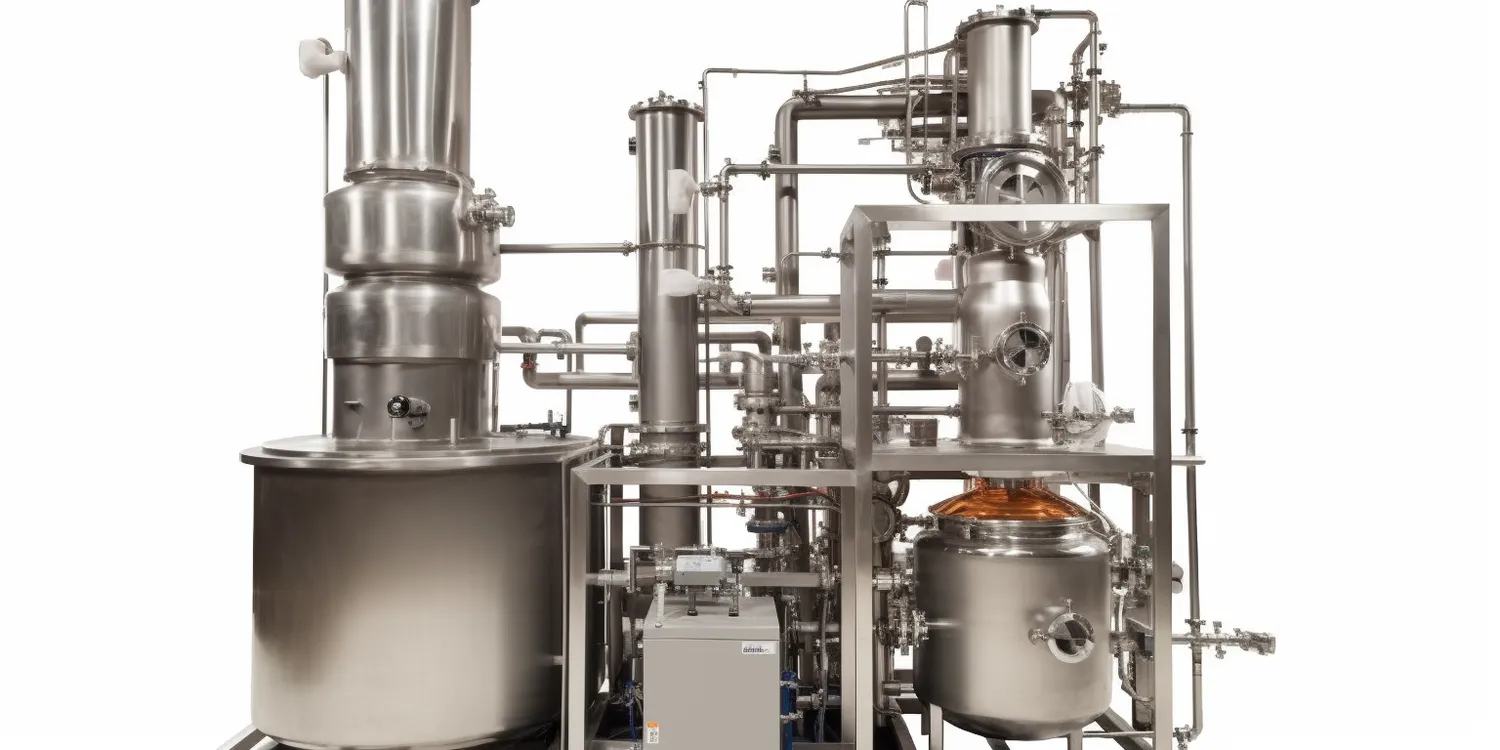
Korzystanie z destylatorów przemysłowych niesie ze sobą wiele korzyści zarówno dla producentów, jak i dla konsumentów. Jedną z głównych zalet jest możliwość uzyskania wysokiej czystości produktów końcowych. Dzięki precyzyjnemu procesowi separacji składników, można otrzymać substancje o wysokiej jakości, co jest szczególnie istotne w branży farmaceutycznej czy spożywczej. Kolejnym atutem jest efektywność energetyczna nowoczesnych destylatorów. Wiele z nich wykorzystuje innowacyjne technologie, które pozwalają na oszczędność energii oraz redukcję kosztów produkcji. Ponadto, automatyzacja procesów destylacji sprawia, że produkcja staje się bardziej niezawodna i mniej czasochłonna.
Jakie są najnowsze technologie w dziedzinie destylacji przemysłowej
W ostatnich latach rozwój technologii związanych z destylacją przemysłową znacząco przyspieszył. Nowoczesne systemy destylacyjne coraz częściej wykorzystują zaawansowane rozwiązania takie jak membrany czy nanotechnologia, co pozwala na jeszcze skuteczniejszą separację składników. Membranowe systemy destylacyjne oferują możliwość separacji substancji przy znacznie niższych temperaturach niż tradycyjne metody, co przekłada się na oszczędności energetyczne oraz mniejsze ryzyko degradacji cennych składników. Innym ciekawym rozwiązaniem są systemy hybrydowe łączące różne metody separacji, takie jak ekstrakcja czy adsorpcja z tradycyjną destylacją. Dzięki temu możliwe jest uzyskanie jeszcze wyższej efektywności procesu oraz lepszej jakości produktów końcowych.
Jakie są kluczowe czynniki wpływające na efektywność destylacji przemysłowej
Efektywność procesu destylacji przemysłowej zależy od wielu czynników, które należy wziąć pod uwagę podczas projektowania i eksploatacji destylatorów. Jednym z najważniejszych elementów jest temperatura, która ma kluczowe znaczenie dla procesu parowania i skraplania. Odpowiednie dobranie temperatury pozwala na maksymalne wykorzystanie różnicy w temperaturach wrzenia poszczególnych składników, co przekłada się na wyższą jakość uzyskiwanego produktu. Kolejnym czynnikiem jest ciśnienie, które również wpływa na temperatury wrzenia substancji. W niektórych przypadkach stosowanie obniżonego ciśnienia może prowadzić do oszczędności energetycznych oraz minimalizacji ryzyka degradacji cennych składników. Ważne jest także odpowiednie dobranie materiałów konstrukcyjnych, które powinny być odporne na działanie wysokich temperatur oraz agresywnych substancji chemicznych.
Jakie są wyzwania związane z użytkowaniem destylatorów przemysłowych
Użytkowanie destylatorów przemysłowych wiąże się z wieloma wyzwaniami, które mogą wpływać na efektywność produkcji oraz jakość uzyskiwanych produktów. Jednym z głównych problemów jest konieczność ciągłego monitorowania i regulacji parametrów pracy urządzeń. Zmiany w składzie surowców czy warunkach atmosferycznych mogą wymagać dostosowania ustawień destylatora, co może być czasochłonne i kosztowne. Dodatkowo, proces destylacji generuje odpady, które muszą być odpowiednio zarządzane, aby zminimalizować ich wpływ na środowisko. Wiele zakładów przemysłowych stara się wdrażać rozwiązania mające na celu recykling odpadów oraz zmniejszenie emisji szkodliwych substancji do atmosfery. Innym wyzwaniem jest utrzymanie wysokiej jakości produktów końcowych w obliczu rosnących wymagań rynkowych oraz regulacji prawnych dotyczących bezpieczeństwa i jakości żywności oraz chemikaliów.
Jakie są zastosowania destylatorów przemysłowych w różnych branżach
Destylatory przemysłowe znajdują szerokie zastosowanie w wielu branżach, co sprawia, że są one niezwykle wszechstronnymi urządzeniami. W przemyśle spożywczym wykorzystuje się je głównie do produkcji alkoholi, takich jak whisky, wódka czy rum. Proces destylacji pozwala na uzyskanie wysokiej czystości trunków oraz ich charakterystycznego smaku i aromatu. W branży farmaceutycznej destylatory służą do produkcji substancji czynnych wykorzystywanych w lekach oraz do oczyszczania rozpuszczalników. Dzięki precyzyjnej separacji składników możliwe jest uzyskanie produktów o wysokiej jakości i czystości, co jest kluczowe w kontekście zdrowia pacjentów. W przemyśle chemicznym destylatory są wykorzystywane do produkcji różnorodnych chemikaliów, takich jak rozpuszczalniki, kwasy czy alkohole organiczne.
Jakie są przyszłościowe kierunki rozwoju technologii destylacyjnej
Przyszłość technologii destylacyjnej zapowiada się bardzo obiecująco dzięki postępowi technologicznemu oraz rosnącym wymaganiom rynku. Wśród najważniejszych kierunków rozwoju można wymienić dalszą automatyzację procesów produkcyjnych, co pozwoli na zwiększenie efektywności oraz redukcję kosztów operacyjnych. Systemy sterowania oparte na sztucznej inteligencji będą mogły dostosowywać parametry pracy urządzeń w czasie rzeczywistym, co przyczyni się do poprawy jakości produktów końcowych. Również rozwój technologii membranowych oraz nanotechnologii otworzy nowe możliwości w zakresie separacji składników cieczy przy niższych temperaturach i ciśnieniach, co wpłynie na oszczędności energetyczne oraz ochronę środowiska. Ponadto coraz większy nacisk kładzie się na zrównoważony rozwój i ekologię, co prowadzi do poszukiwania innowacyjnych rozwiązań mających na celu minimalizację negatywnego wpływu procesów przemysłowych na środowisko naturalne.
Jakie są kluczowe aspekty bezpieczeństwa przy pracy z destylatorami przemysłowymi
Bezpieczeństwo pracy z destylatorami przemysłowymi jest niezwykle istotnym zagadnieniem, które należy uwzględnić zarówno podczas projektowania instalacji, jak i jej eksploatacji. Przede wszystkim ważne jest zapewnienie odpowiednich warunków pracy dla personelu obsługującego urządzenia. Należy zadbać o szkolenia pracowników dotyczące zasad BHP oraz procedur awaryjnych w przypadku wystąpienia nieprzewidzianych sytuacji. Kolejnym kluczowym aspektem jest regularna konserwacja i inspekcja sprzętu, co pozwala na wykrycie ewentualnych usterek przed ich eskalacją. Ważne jest także stosowanie odpowiednich materiałów budowlanych odpornych na działanie wysokich temperatur oraz agresywnych substancji chemicznych. Systemy wentylacyjne powinny być dostosowane do specyfiki procesu produkcyjnego, aby minimalizować ryzyko wystąpienia pożaru lub eksplozji.
Jakie są koszty związane z inwestycją w destylatory przemysłowe
Inwestycja w destylatory przemysłowe wiąże się z różnorodnymi kosztami, które należy uwzględnić podczas planowania zakupu takiego urządzenia. Koszt samego sprzętu może znacznie się różnić w zależności od jego rodzaju, wielkości oraz zastosowanej technologii. Na przykład nowoczesne kolumnowe destylatory będą droższe od prostszych modeli przeznaczonych do mniejszych zakładów produkcyjnych. Oprócz kosztu zakupu należy również uwzględnić wydatki związane z instalacją urządzenia oraz jego uruchomieniem. Koszty te mogą obejmować prace budowlane, montaż instalacji elektrycznych czy hydraulicznych oraz szkolenie personelu obsługującego urządzenie. Dodatkowo warto rozważyć koszty eksploatacyjne związane z utrzymaniem sprzętu w dobrym stanie technicznym oraz zużyciem energii potrzebnej do jego pracy.
Jakie są kluczowe trendy w branży destylacyjnej na świecie
Branża destylacyjna na świecie przechodzi dynamiczne zmiany, które są wynikiem rosnących oczekiwań konsumentów oraz postępu technologicznego. W ostatnich latach zauważalny jest trend w kierunku produkcji alkoholi rzemieślniczych, co prowadzi do wzrostu zapotrzebowania na mniejsze, bardziej elastyczne destylatory. Ponadto, coraz większą uwagę przykłada się do zrównoważonego rozwoju, co skutkuje poszukiwaniem ekologicznych metod produkcji oraz surowców pochodzących z odnawialnych źródeł. Wzrost znaczenia zdrowego stylu życia wpływa także na rozwój destylacji niskoprocentowych alkoholi oraz napojów bezalkoholowych.