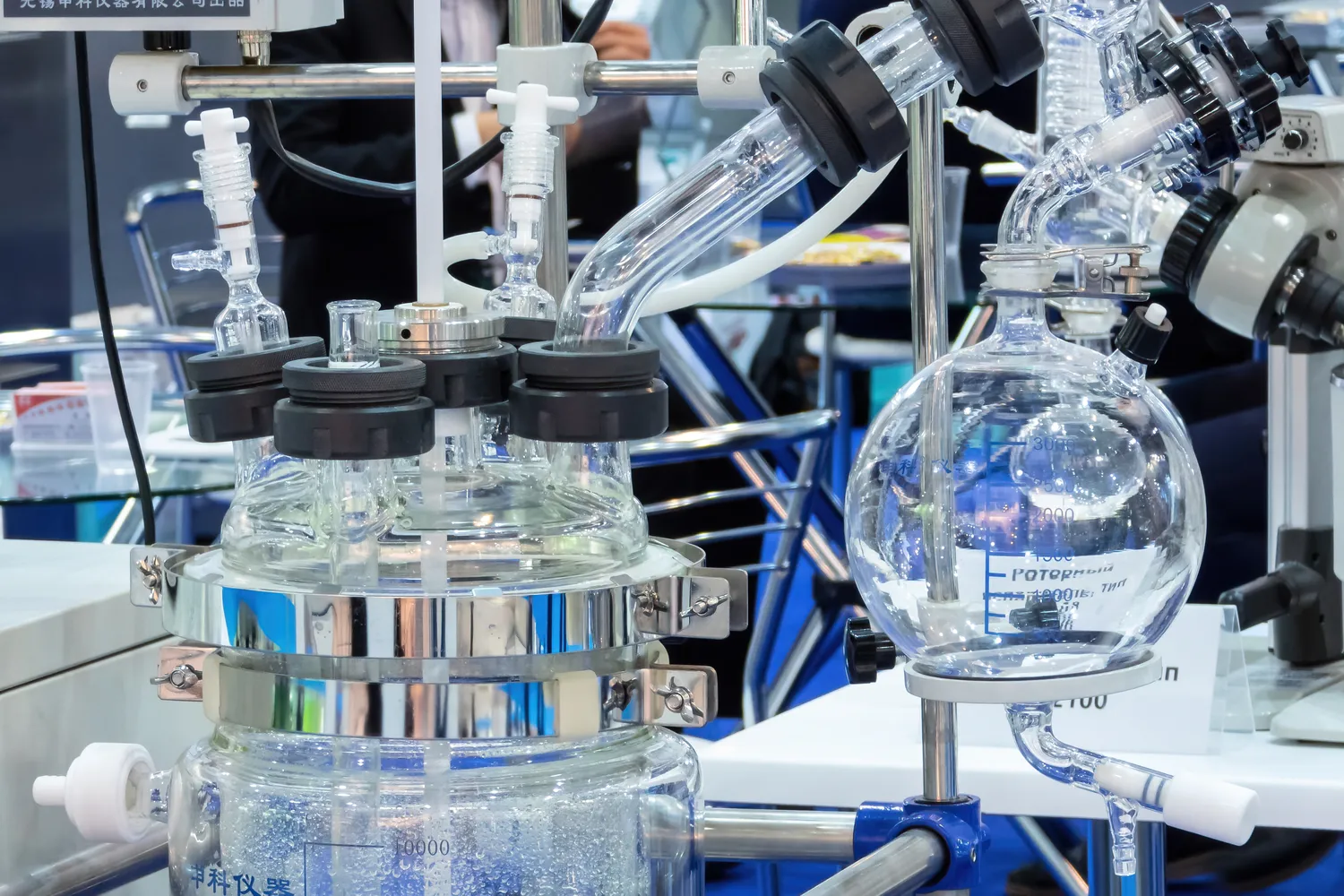
Destylacja rozpuszczalników to proces separacji cieczy, który wykorzystuje różnice w temperaturze wrzenia różnych substancji. Jest to jedna z najstarszych i najczęściej stosowanych metod oczyszczania oraz wydobywania czystych składników z mieszanin. W praktyce polega na podgrzewaniu cieczy, co prowadzi do jej parowania, a następnie skraplaniu powstałej pary. Dzięki temu można oddzielić substancje o różnych temperaturach wrzenia, co jest szczególnie przydatne w chemii oraz przemyśle farmaceutycznym. Proces ten może być przeprowadzany w różnych warunkach, w tym pod ciśnieniem atmosferycznym lub w próżni, co pozwala na uzyskanie lepszej efektywności. Destylacja rozpuszczalników jest nie tylko skuteczna, ale także stosunkowo prosta do przeprowadzenia, co czyni ją popularnym wyborem w laboratoriach oraz zakładach przemysłowych.
Jakie są zastosowania destylacji rozpuszczalników w przemyśle
Destylacja rozpuszczalników znajduje szerokie zastosowanie w różnych gałęziach przemysłu, od chemicznego po spożywczy. W przemyśle chemicznym proces ten jest kluczowy dla oczyszczania surowców oraz produkcji wysokiej jakości substancji chemicznych. Na przykład, w produkcji alkoholu etylowego destylacja pozwala na oddzielenie czystego alkoholu od pozostałych składników fermentacji. W przemyśle farmaceutycznym destylacja jest wykorzystywana do oczyszczania substancji czynnych oraz usuwania niepożądanych zanieczyszczeń. Ponadto w przemyśle petrochemicznym proces ten jest niezbędny do separacji różnych frakcji ropy naftowej, co umożliwia produkcję paliw oraz innych produktów naftowych. W branży spożywczej destylacja stosowana jest do produkcji olejków eterycznych oraz aromatów, które są wykorzystywane w przemyśle spożywczym i kosmetycznym.
Jakie są różnice między destylacją prostą a frakcyjną
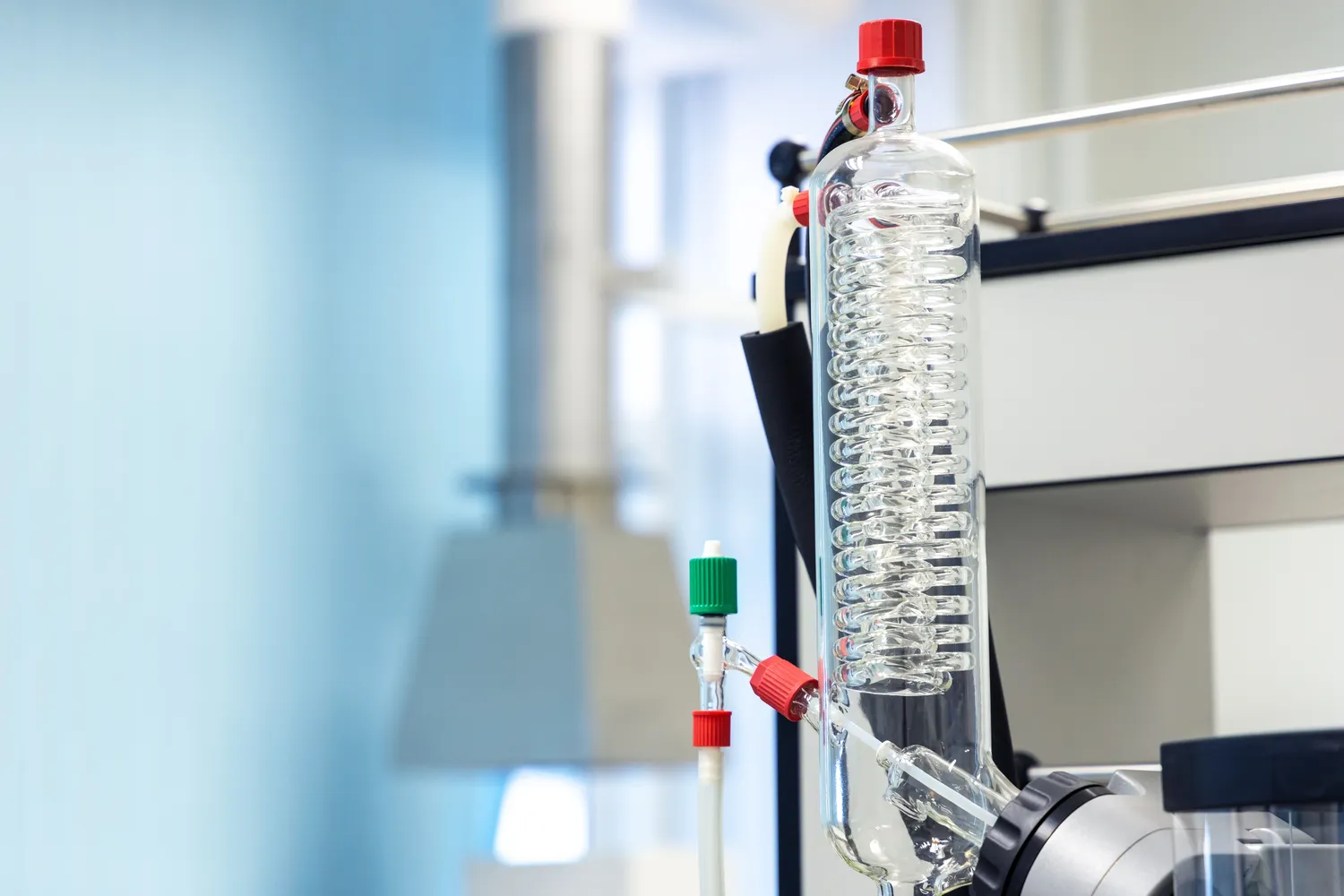
Destylacja prosta i frakcyjna to dwa podstawowe typy procesu destylacji, które różnią się zasadniczo pod względem zastosowania oraz efektywności separacji składników. Destylacja prosta jest najprostszą formą tego procesu i polega na jednorazowym podgrzewaniu mieszaniny cieczy do momentu jej wrzenia, a następnie skraplaniu pary. Jest ona skuteczna jedynie wtedy, gdy różnica temperatur wrzenia pomiędzy składnikami jest znaczna. Z kolei destylacja frakcyjna jest bardziej zaawansowaną techniką, która umożliwia separację składników o zbliżonych temperaturach wrzenia poprzez wielokrotne skraplanie i parowanie. W tym przypadku używa się kolumny frakcyjnej, która zwiększa powierzchnię wymiany ciepła i pozwala na bardziej efektywne oddzielanie poszczególnych składników. Destylacja frakcyjna znajduje zastosowanie tam, gdzie wymagana jest wysoka czystość produktu końcowego oraz precyzyjna separacja składników o podobnych właściwościach fizykochemicznych.
Jakie są najważniejsze urządzenia do destylacji rozpuszczalników
W procesie destylacji rozpuszczalników kluczowe znaczenie mają odpowiednie urządzenia, które zapewniają skuteczność i bezpieczeństwo tego procesu. Najważniejszym elementem jest aparat destylacyjny, który może mieć różne formy w zależności od rodzaju destylacji. W przypadku destylacji prostej najczęściej stosuje się kolbę okrągłodenna oraz chłodnicę do skraplania pary. W przypadku bardziej skomplikowanej destylacji frakcyjnej niezbędna jest kolumna frakcyjna, która zwiększa efektywność separacji dzięki wielokrotnemu skraplaniu i parowaniu cieczy. Dodatkowo ważnymi elementami są źródła ciepła, takie jak piec lub grzałka elektryczna, które muszą być dostosowane do wymagań konkretnego procesu. Oprócz tego istotne są także systemy monitorujące temperaturę oraz ciśnienie wewnętrzne aparatu destylacyjnego, co pozwala na optymalizację procesu i zwiększenie jego bezpieczeństwa.
Jakie czynniki wpływają na efektywność destylacji rozpuszczalników
Efektywność destylacji rozpuszczalników jest uzależniona od wielu czynników, które mogą znacząco wpłynąć na jakość i ilość uzyskiwanego produktu. Kluczowym aspektem jest różnica w temperaturach wrzenia składników, ponieważ im większa ta różnica, tym łatwiejsze jest ich oddzielenie. W przypadku substancji o zbliżonych temperaturach wrzenia, proces może być znacznie trudniejszy i wymaga zastosowania bardziej zaawansowanych technik, takich jak destylacja frakcyjna. Kolejnym istotnym czynnikiem jest ciśnienie atmosferyczne, które wpływa na temperaturę wrzenia cieczy. W obniżonym ciśnieniu substancje mogą wrzeć w niższej temperaturze, co jest szczególnie korzystne dla termolabilnych związków chemicznych. Również szybkość podgrzewania ma znaczenie; zbyt szybkie podgrzewanie może prowadzić do niekontrolowanego parowania i utraty cennych składników. Oprócz tego, jakość używanych urządzeń oraz ich odpowiednia kalibracja mają kluczowe znaczenie dla osiągnięcia optymalnych wyników.
Jakie są zalety i wady destylacji rozpuszczalników
Destylacja rozpuszczalników ma wiele zalet, które przyczyniają się do jej popularności w różnych gałęziach przemysłu oraz laboratoriach. Jedną z głównych zalet jest jej efektywność w separacji składników o różnych temperaturach wrzenia. Proces ten pozwala na uzyskanie wysokiej czystości produktów końcowych, co jest szczególnie istotne w przemyśle farmaceutycznym oraz chemicznym. Dodatkowo destylacja jest stosunkowo prostą metodą, która nie wymaga skomplikowanych technologii ani drogich materiałów eksploatacyjnych. Jednakże, jak każda metoda, ma także swoje wady. Proces destylacji może być czasochłonny, zwłaszcza w przypadku substancji o zbliżonych temperaturach wrzenia, co wymaga zastosowania kolumn frakcyjnych i wielokrotnego skraplania. Ponadto niektóre substancje mogą ulegać rozkładowi pod wpływem wysokiej temperatury, co ogranicza możliwość ich oczyszczania tą metodą.
Jakie są alternatywy dla destylacji rozpuszczalników
Chociaż destylacja rozpuszczalników jest jedną z najczęściej stosowanych metod separacji cieczy, istnieją również inne techniki, które mogą być wykorzystywane w zależności od specyfiki procesu oraz wymaganych rezultatów. Jedną z alternatyw jest ekstrakcja rozpuszczalnikowa, która polega na wykorzystaniu innego rozpuszczalnika do wydobycia pożądanych składników z mieszaniny. Ta metoda jest często stosowana w przemyśle spożywczym oraz farmaceutycznym do pozyskiwania olejków eterycznych czy substancji czynnych z roślin. Inną popularną techniką jest chromatografia, która umożliwia separację składników na podstawie ich różnic w powinowactwie do fazy stacjonarnej i ruchomej. Chromatografia może być stosowana zarówno w laboratoriach analitycznych, jak i w procesach przemysłowych do oczyszczania substancji chemicznych. Dodatkowo można wspomnieć o membranowych metodach separacji, takich jak osmoza odwrotna czy ultrafiltracja, które są coraz częściej wykorzystywane w przemyśle chemicznym oraz wodociągowym.
Jakie są najczęstsze błędy podczas destylacji rozpuszczalników
Podczas przeprowadzania procesu destylacji rozpuszczalników istnieje wiele pułapek i błędów, które mogą prowadzić do nieefektywności lub nawet uszkodzenia sprzętu. Jednym z najczęstszych błędów jest niewłaściwe ustawienie temperatury podgrzewania. Zbyt wysoka temperatura może prowadzić do niekontrolowanego parowania i utraty cennych składników, natomiast zbyt niska temperatura może skutkować niedostatecznym oddzieleniem składników. Kolejnym problemem jest niewłaściwe dobranie aparatu destylacyjnego; użycie kolby zamiast kolumny frakcyjnej w przypadku substancji o podobnych temperaturach wrzenia może znacznie obniżyć efektywność procesu. Niezbędne jest również monitorowanie ciśnienia wewnętrznego aparatu; jego zmiany mogą wpłynąć na temperaturę wrzenia i skuteczność separacji. Często popełnianym błędem jest także brak odpowiedniej kalibracji urządzeń pomiarowych oraz ignorowanie czystości używanych surowców, co może prowadzić do kontaminacji produktu końcowego.
Jakie są przyszłe kierunki badań nad destylacją rozpuszczalników
Przyszłość badań nad destylacją rozpuszczalników koncentruje się na zwiększeniu efektywności tego procesu oraz minimalizacji jego wpływu na środowisko naturalne. W ostatnich latach pojawiły się nowe technologie i podejścia mające na celu optymalizację tradycyjnych metod destylacji. Badania nad zastosowaniem nanotechnologii w konstrukcji kolumn frakcyjnych mogą przyczynić się do zwiększenia powierzchni wymiany ciepła oraz poprawy efektywności separacji składników o podobnych właściwościach fizykochemicznych. Ponadto rozwijane są nowe materiały absorbujące oraz membrany filtracyjne, które mogą zastąpić tradycyjne metody separacji i przyczynić się do zmniejszenia zużycia energii podczas procesu destylacji. Istotnym kierunkiem badań są także technologie związane z odzyskiem energii oraz recyklingiem rozpuszczalników, co wpisuje się w globalne trendy związane z ochroną środowiska i zrównoważonym rozwojem przemysłu chemicznego.
Jakie są najważniejsze aspekty bezpieczeństwa w destylacji rozpuszczalników
Bezpieczeństwo w procesie destylacji rozpuszczalników jest kluczowym zagadnieniem, które wymaga szczególnej uwagi ze względu na ryzyko związane z wysokimi temperaturami oraz używaniem substancji chemicznych. Przede wszystkim, należy zapewnić odpowiednią wentylację w pomieszczeniach, gdzie przeprowadzany jest proces destylacji, aby uniknąć gromadzenia się oparów, które mogą być łatwopalne lub toksyczne. Używanie odpowiednich środków ochrony osobistej, takich jak rękawice, gogle ochronne oraz odzież robocza, jest niezbędne dla ochrony pracowników przed potencjalnymi zagrożeniami. Ważne jest także regularne przeprowadzanie przeglądów technicznych urządzeń destylacyjnych oraz ich konserwacja, aby zapobiec awariom i wyciekom. Warto również wdrożyć procedury awaryjne na wypadek pożaru lub wycieku substancji chemicznych, co pozwoli na szybką reakcję i minimalizację skutków.