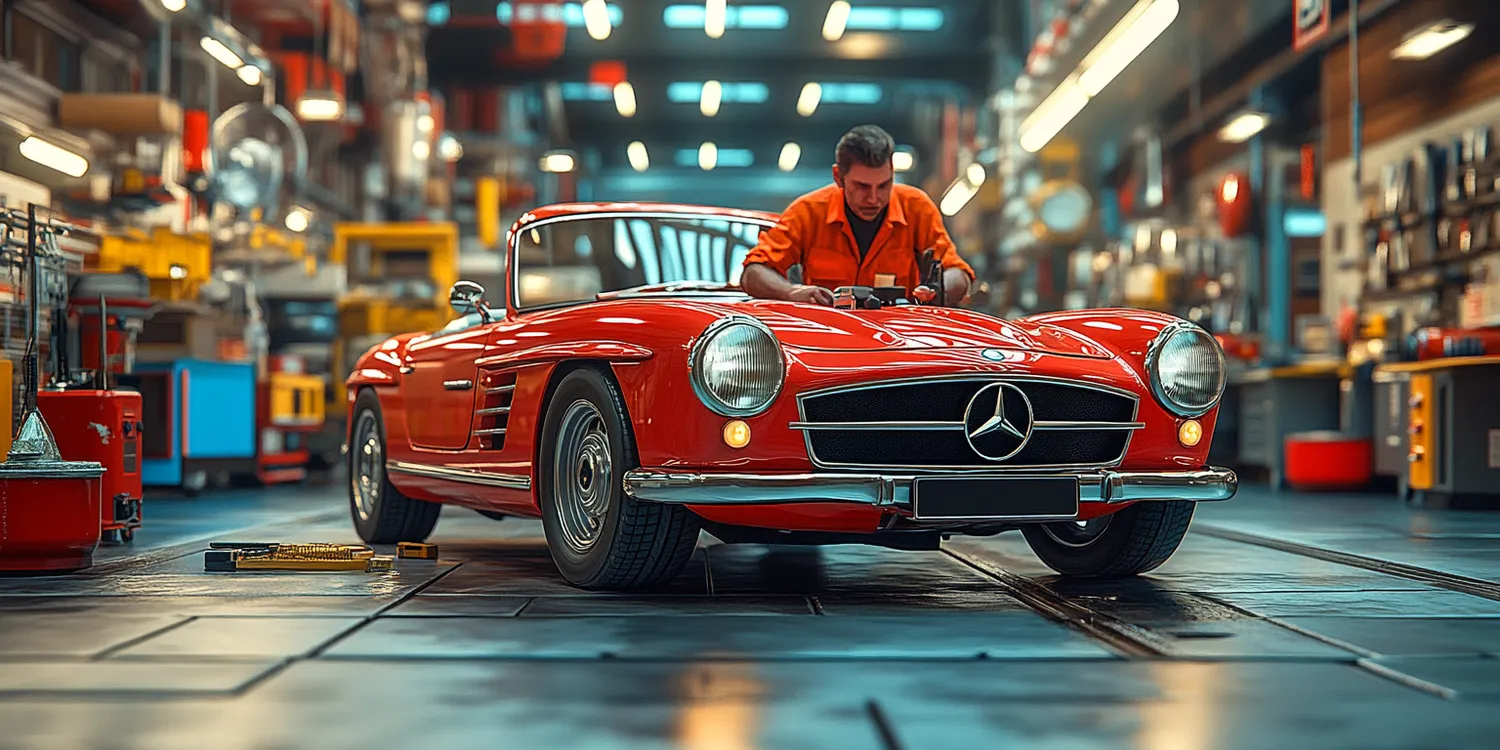
Łączenie dwóch kompresorów to proces, który wymaga staranności i zrozumienia zasad działania tych urządzeń. Przede wszystkim należy zwrócić uwagę na ich parametry techniczne, takie jak wydajność, ciśnienie robocze oraz rodzaj napędu. W przypadku kompresorów tłokowych, ważne jest, aby były one zgodne pod względem wydajności, co pozwoli na efektywne współdziałanie. Warto także rozważyć zastosowanie odpowiednich złączek i węży, które będą w stanie wytrzymać ciśnienie generowane przez oba urządzenia. Kolejnym krokiem jest zaplanowanie układu instalacji, aby zapewnić optymalny przepływ powietrza oraz minimalizować straty energii. Należy również pamiętać o odpowiednim zabezpieczeniu systemu przed przeciążeniem, co może prowadzić do uszkodzenia kompresorów. Dobrze jest także przemyśleć kwestię wentylacji, aby uniknąć przegrzewania się urządzeń podczas pracy.
Jakie są zalety łączenia dwóch kompresorów?
Łączenie dwóch kompresorów niesie ze sobą szereg korzyści, które mogą znacząco poprawić efektywność pracy w różnych zastosowaniach. Przede wszystkim zwiększa to ogólną wydajność systemu pneumatycznego, co jest szczególnie istotne w przemyśle oraz warsztatach zajmujących się obróbką metali czy innymi procesami wymagającymi dużych ilości sprężonego powietrza. Dzięki połączeniu dwóch jednostek można uzyskać wyższe ciśnienie robocze oraz większą ilość sprężonego powietrza dostępnego w danym momencie. To z kolei pozwala na równoczesne zasilanie kilku narzędzi pneumatycznych lub maszyn, co zwiększa wydajność produkcji. Dodatkowo, w przypadku awarii jednego z kompresorów, drugi może przejąć jego funkcje, co zapewnia ciągłość pracy i minimalizuje przestoje. Warto również wspomnieć o oszczędnościach energetycznych, jakie mogą wyniknąć z optymalizacji pracy obu urządzeń poprzez ich synchronizację.
Jakie są najczęstsze błędy przy łączeniu kompresorów?
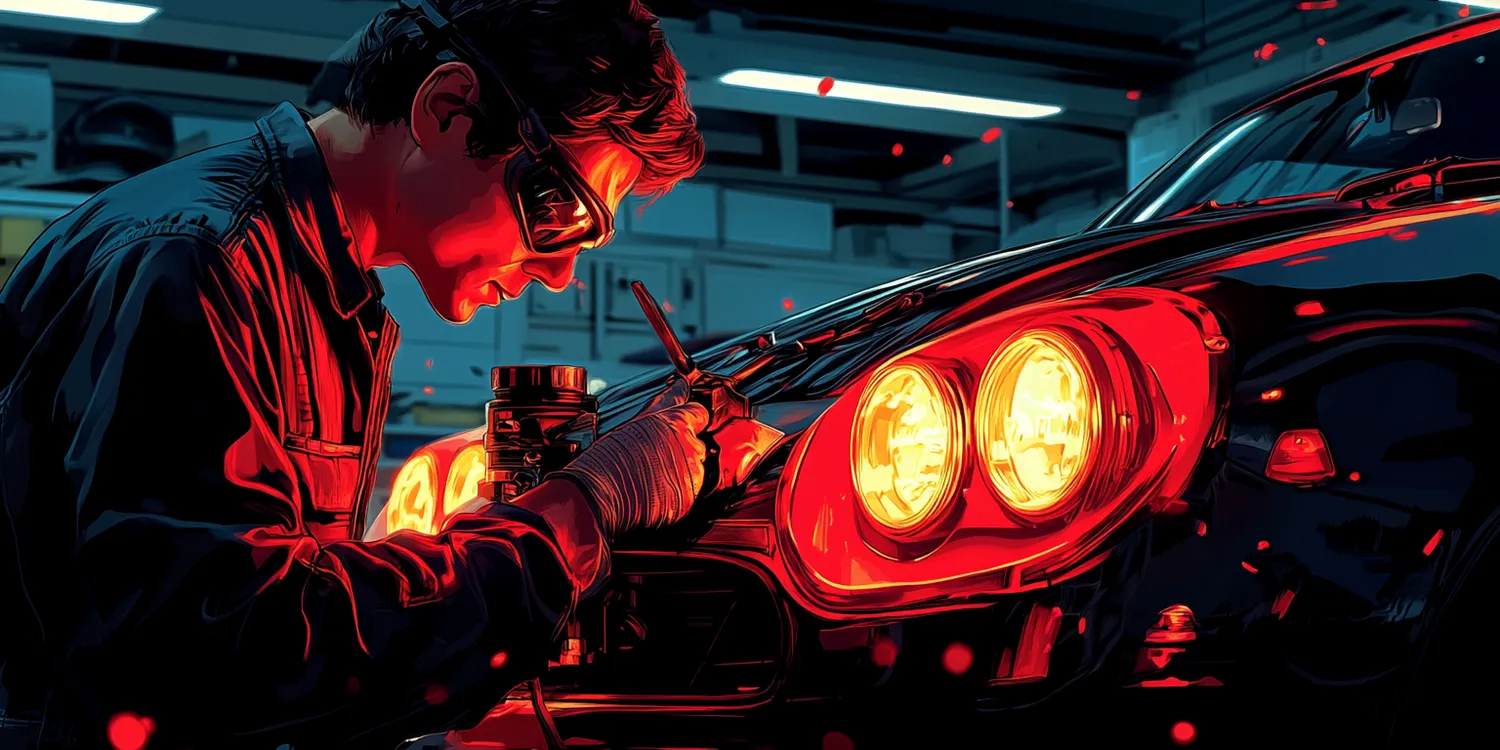
Podczas łączenia dwóch kompresorów istnieje wiele pułapek, które mogą prowadzić do problemów z działaniem całego systemu. Jednym z najczęstszych błędów jest niewłaściwe dobranie parametrów technicznych obu urządzeń. Jeśli jeden kompresor ma znacznie wyższą wydajność niż drugi, może to prowadzić do nierównomiernego obciążenia i szybszego zużycia słabszej jednostki. Innym powszechnym problemem jest niewłaściwe wykonanie instalacji pneumatycznej, co może skutkować wyciekami powietrza lub spadkiem ciśnienia w systemie. Często zdarza się także ignorowanie kwestii wentylacji i chłodzenia kompresorów, co może prowadzić do ich przegrzewania się i awarii. Niektórzy użytkownicy zapominają o regularnym serwisowaniu urządzeń oraz kontroli stanu filtrów powietrza i oleju, co również wpływa na ich wydajność i żywotność.
Jakie materiały są potrzebne do połączenia kompresorów?
Aby skutecznie połączyć dwa kompresory, konieczne jest zgromadzenie odpowiednich materiałów i narzędzi. Przede wszystkim potrzebne będą wysokiej jakości węże pneumatyczne o odpowiedniej średnicy oraz złączki umożliwiające bezpieczne połączenie obu jednostek. Warto zwrócić uwagę na materiały odporne na wysokie ciśnienie oraz działanie oleju i innych substancji chemicznych. Dodatkowo przydatne będą różnego rodzaju zawory regulacyjne oraz filtry powietrza, które pomogą w utrzymaniu czystości sprężonego powietrza oraz stabilności ciśnienia w systemie. Niezbędne będą także narzędzia montażowe takie jak klucze nasadowe czy śrubokręty do precyzyjnego dokręcania połączeń. W zależności od specyfiki instalacji mogą być potrzebne także dodatkowe elementy takie jak manometry do pomiaru ciśnienia czy automatyczne sterowniki do zarządzania pracą obu kompresorów.
Jakie są różnice między kompresorami tłokowymi a śrubowymi?
Wybór odpowiedniego typu kompresora do połączenia ma kluczowe znaczenie dla efektywności całego systemu. Kompresory tłokowe i śrubowe różnią się zasadniczo pod względem konstrukcji, wydajności oraz zastosowania. Kompresory tłokowe działają na zasadzie ruchu tłoka w cylindrze, co pozwala na sprężanie powietrza. Są one zazwyczaj tańsze w zakupie i łatwiejsze w serwisowaniu, co czyni je popularnym wyborem w małych warsztatach oraz do zastosowań domowych. Ich wadą jest jednak mniejsza wydajność przy dużych obciążeniach oraz głośniejsza praca. Z kolei kompresory śrubowe charakteryzują się wyższą wydajnością oraz cichszą pracą, co sprawia, że są idealne do dużych zakładów przemysłowych, gdzie wymagane są długotrwałe operacje z dużymi ilościami sprężonego powietrza. Warto również zauważyć, że kompresory śrubowe mają tendencję do lepszego zarządzania temperaturą pracy, co przekłada się na ich dłuższą żywotność.
Jakie są najlepsze praktyki przy łączeniu kompresorów?
Aby zapewnić prawidłowe działanie połączonych kompresorów, warto stosować się do kilku najlepszych praktyk. Przede wszystkim należy dokładnie zaplanować cały proces instalacji, uwzględniając wszystkie parametry techniczne obu urządzeń. Ważne jest, aby przed przystąpieniem do montażu przeprowadzić dokładną analizę wymagań dotyczących ciśnienia i wydajności, aby uniknąć problemów związanych z niewłaściwym doborem sprzętu. Kolejnym krokiem jest staranne wykonanie wszystkich połączeń pneumatycznych, z użyciem odpowiednich narzędzi i materiałów, które zapewnią szczelność systemu. Należy również regularnie kontrolować stan filtrów powietrza oraz oleju, aby utrzymać wysoką jakość sprężonego powietrza. Dobrze jest także wprowadzić procedury monitorowania pracy kompresorów, co pozwoli na szybką reakcję w przypadku jakichkolwiek nieprawidłowości. Nie można zapominać o regularnym serwisowaniu urządzeń, co pomoże w utrzymaniu ich w dobrym stanie przez długi czas.
Jakie są koszty związane z łączeniem kompresorów?
Koszty związane z łączeniem dwóch kompresorów mogą się znacznie różnić w zależności od wielu czynników, takich jak rodzaj urządzeń, materiały potrzebne do instalacji oraz ewentualne koszty robocizny. Przy zakupie nowych kompresorów warto zwrócić uwagę na ich parametry techniczne oraz ceny rynkowe, ponieważ mogą one znacząco wpłynąć na całkowity koszt inwestycji. Dodatkowo należy uwzględnić wydatki związane z zakupem niezbędnych akcesoriów, takich jak węże pneumatyczne, złączki czy zawory regulacyjne. Koszty te mogą być znaczne, zwłaszcza jeśli planuje się użycie wysokiej jakości komponentów. Warto również rozważyć ewentualne wydatki na serwisowanie i konserwację systemu po jego uruchomieniu, co może wpłynąć na długoterminową efektywność działania kompresorów. Ostatecznie koszt łączenia dwóch kompresorów powinien być postrzegany jako inwestycja w zwiększenie wydajności produkcji oraz poprawę jakości wykonywanych prac.
Jakie są najczęstsze zastosowania połączonych kompresorów?
Połączone kompresory znajdują szerokie zastosowanie w różnych branżach przemysłowych oraz usługowych. Jednym z najpopularniejszych zastosowań jest przemysł budowlany, gdzie sprężone powietrze jest wykorzystywane do zasilania narzędzi pneumatycznych takich jak młoty udarowe czy wiertarki. Dzięki większej wydajności połączonych jednostek możliwe jest równoczesne zasilanie kilku narzędzi bez obawy o spadek ciśnienia roboczego. Kolejnym istotnym obszarem jest przemysł motoryzacyjny, gdzie sprężone powietrze służy do obsługi różnych maszyn i urządzeń wykorzystywanych w warsztatach samochodowych. Połączone kompresory są również często stosowane w procesach produkcyjnych wymagających dużych ilości sprężonego powietrza do transportu materiałów lub chłodzenia maszyn. W branży spożywczej sprężone powietrze znajduje zastosowanie przy pakowaniu produktów czy też w procesach mycia i dezynfekcji linii produkcyjnych.
Jakie technologie wspierają efektywność pracy kompresorów?
Współczesne technologie znacząco wpływają na efektywność pracy kompresorów oraz ich integrację w systemy pneumatyczne. Jednym z kluczowych elementów jest automatyka przemysłowa, która pozwala na monitorowanie i zarządzanie pracą kompresorów w czasie rzeczywistym. Dzięki zastosowaniu czujników ciśnienia i temperatury możliwe jest optymalne dostosowanie pracy urządzeń do aktualnych potrzeb produkcyjnych. Systemy zarządzania energią pomagają natomiast w redukcji kosztów eksploatacyjnych poprzez optymalizację zużycia energii elektrycznej przez kompresory. Również nowoczesne rozwiązania informatyczne umożliwiają zdalne monitorowanie pracy urządzeń oraz diagnostykę ich stanu technicznego, co pozwala na szybsze reagowanie na ewentualne awarie czy problemy operacyjne. Inwestycje w technologie takie jak inwertery czy systemy odzysku ciepła mogą dodatkowo zwiększyć efektywność energetyczną całego systemu pneumatycznego.
Jakie są wyzwania związane z łączeniem dwóch kompresorów?
Łączenie dwóch kompresorów wiąże się z pewnymi wyzwaniami technicznymi oraz organizacyjnymi, które należy uwzględnić podczas planowania takiego przedsięwzięcia. Przede wszystkim kluczowym wyzwaniem jest zapewnienie odpowiedniej synchronizacji pracy obu urządzeń, aby uniknąć sytuacji przeciążenia jednego z nich lub niewłaściwego rozdziału obciążenia między nimi. Konieczne może być zastosowanie zaawansowanych systemów sterujących lub automatyki przemysłowej, które pozwolą na optymalne zarządzanie pracą obu jednostek. Kolejnym wyzwaniem jest konieczność dostosowania instalacji pneumatycznej do specyfiki obu kompresorów oraz zapewnienie szczelności wszystkich połączeń, co może wymagać specjalistycznej wiedzy i doświadczenia. Należy również pamiętać o regularnym serwisowaniu i konserwacji połączonych urządzeń, aby uniknąć problemów związanych z ich awariami czy spadkiem wydajności.